Наверняка остались ещё люди, которые думают, что «акценты» в Казахстан приходят напрямую из Кореи. Но это не так. Значительная часть модельного ряда Hyundai собирается у нас под боком, а именно в России. Нас пригласили на завод «Хёндэ Мотор Мануфактуринг Рус» (HMMR) и показали, как делают автомобили, колесящие по дорогам СНГ.
Осенью 2010 года в Санкт-Петербурге начало свою работу предприятие «Хёндэ Мотор Мануфактуринг Рус». Этот завод стал седьмым зарубежным проектом для корейской марки. Ещё машины Hyundai собирают в США, Китае, Индии, Турции, Бразилии и даже в Чехии. Стоит отметить, что производство в Питере, как и на вышеперечисленных заводах, идёт по полному циклу, то есть начинается всё с обычного листа металла, а заканчивается готовым автомобилем. Одним из нескольких, если быть точнее. В цехах можно заметить Hyundai Solaris (Accent на рынке Казахстана), новый кроссовер Creta, а также Kia Rio, как седан, так и хэтч. Раньше на HMMR собирали и хэтчбек Solaris, но от него пришлось отказаться в пользу «Креты».
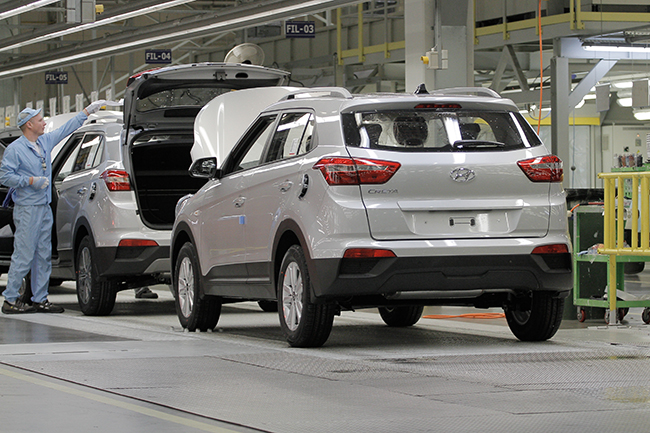
Всего на создание одного автомобиля на заводе тратится около 18 часов. Половина этого времени уходит на покраску. Ежедневно с конвейера завода сходит 900 машин, а это, учитывая длину рабочего дня и количество смен, означает 43 авто в час. Собираются они усилиями 1 900 человек персонала. Это на 700 человек больше, чем на аналогичном заводе в корейском Асане, где мы побывали в 2014 году, хотя производственная мощность российского предприятия меньше. В год оно способно выпустить 200 000 машин против 278 000 в Корее. Тем не менее казахстанскому автопрому даже до таких показателей ещё далеко. В Питере собирают на 54 % больше авто, чем весь казахстанский автопром в предкризисном 2014 году.
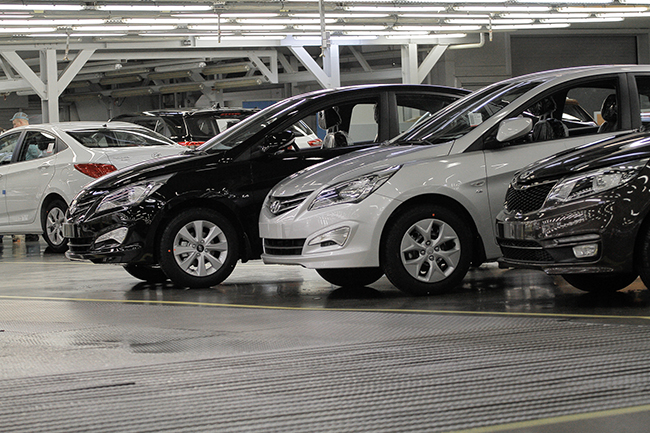
Ну а теперь давайте поговорим непосредственно о производстве. Как я уже упоминал выше, завод делает машины по полному циклу, то есть авто начинает свою жизнь как лист металла. В цехе штамповки его превращают в несколько деталей. Делает это огромный пресс, который работает практически без человеческого участия.
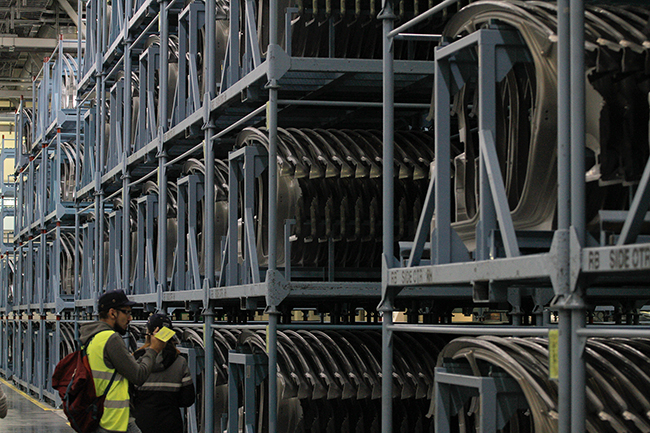
Люди лишь следят за процессом и вклиниваются в него только в случае каких-либо ошибок или неисправностей. Основные части, штампуемые прессом, это, конечно же, днище, боковины и крыша. Из них на огромном сварочном стенде — он, к слову, тоже самостоятельный — получается кузов авто.
HMMR в цифрах
43 автомобиля в час
900 машин в день
200 000 единиц в год
порядка 2.2 тысяч человек персонала
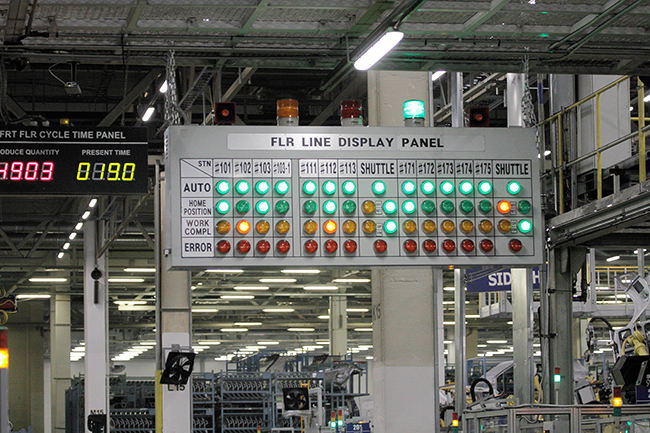
К сожалению, увидеть во всей красе процесс не представляется возможным. Забота о жизни и здоровье персонала не позволяет подходить слишком близко к роботам. Их в сварочном цехе целых 180 штук, и кто его знает, что эти «ребята» думают. Интересный факт: на машинах, производимых на этом заводе, от 4 500 до 6 200 точек сварки, и лишь за малую их часть ответственны люди.
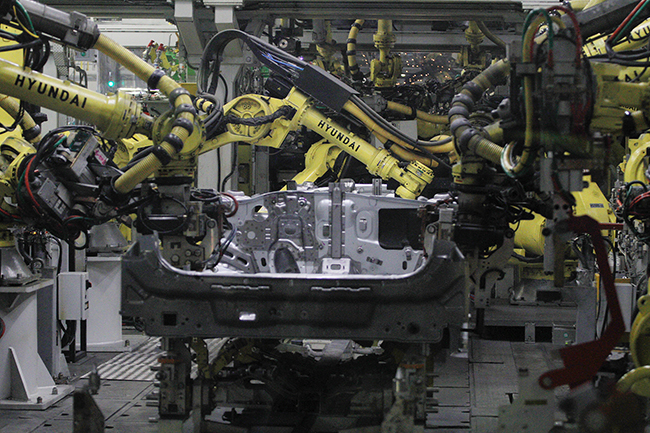
По окончании сварочных работ готовый кузов отправляется на окраску. Доступ в эту часть завода имеет весьма узкий круг людей, и мы в этот список почему-то не попали. Фактически цех окраски стал единственным секретным местом на питерском предприятии. На Asan Plant ограничений было побольше, к примеру корейцы ещё и своих роботов запрещали снимать. Да-да, в «Хёндэ» сами делают роботов, которые собирают их автомобили.
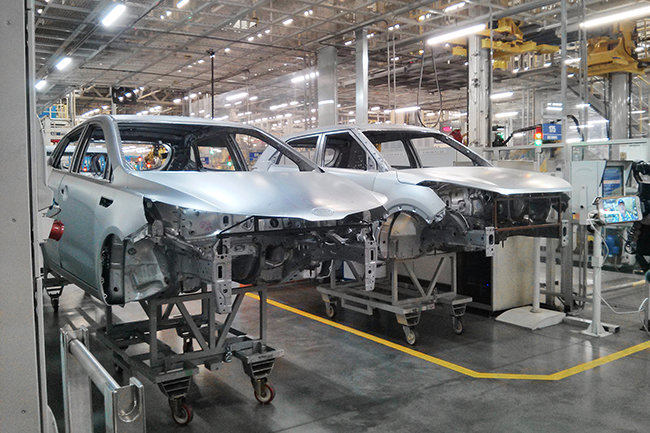
На окраске машина проводит 8 часов. За это время кузов чистят, наносят антикоррозийку, грунтуют и наконец-таки наносят краску. На выходе мы имеем полностью собранный и окрашенный кузов, который в следующем цехе снова частично разбирают, одевают в защитные чехлы, чтобы избежать повреждений свежей краски, и потихоньку начинают превращать в полноценный автомобиль.
Откуда берутся детали
Часть комплектующих для автомобилей, собираемых в Питере, делается чуть ли не в шаговой доступности от завода. В частности, это касается внешнего пластикового обвеса и торпедо. А вот более серьёзные детали, моторы к примеру, поставляются из-за рубежа. В случае с двигателями речь идёт о Китае. А вот завод Mitsubishi в Калуге, к примеру, получал часть агрегатов из Таиланда
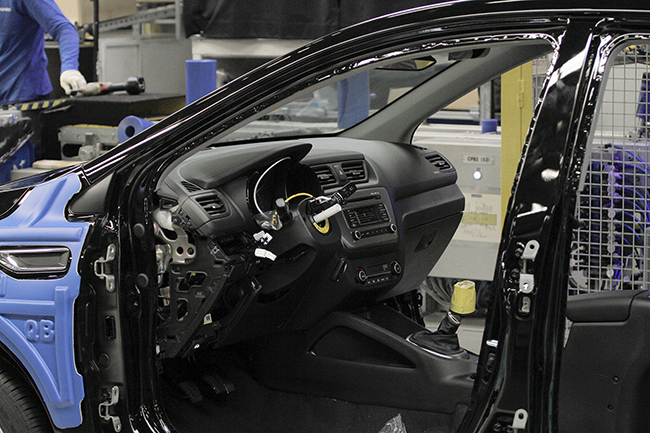
Если во время штамповки, сварки и окраски кузова основную работу выполняют роботы, то на постах сборочного цеха бал правят люди. В первую очередь операторы сканируют VIN-код автомобиля, который был нанесён на кузов сразу после сварки. Так сборщики узнают, какую именно комплектацию имеет авто и что в него ставить. С каждой пройденной на конвейере станцией кузова обрастают новыми деталями, тогда как на отдельной линии мастера комплектуют двери электроникой, обшивками и стёклами.
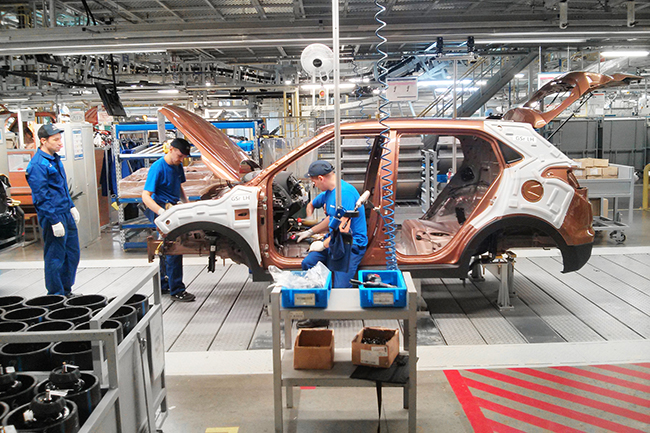
Какого-то конкретного порядка движения авто по конвейеру нет. То есть сборщик может в любой момент столкнуться как с «Акцентом», так и с «Рио» либо же с «Кретой» и при этом ничего не перепутать, ну, по крайней мере, Creta с фарами от Accent’а или Rio мы пока не видели.
Как не заскучать
Монотонность работы действительно может стать проблемой. Именно поэтому спецов каждые несколько часов меняют местами. В этом есть ещё один приятный бонус: чем больше станций освоит оператор, тем более ценным кадром он становится, что напрямую сказывается на его зарплате. В среднем операторы получают около 230 тысяч в пересчёте на наши деньги.
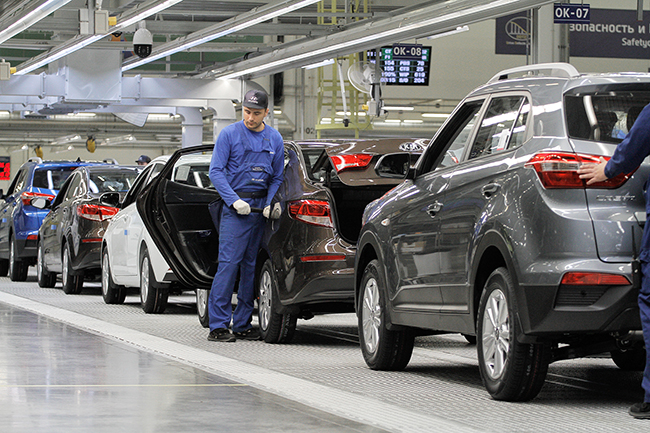
По завершении сборки автомобиль ждёт весьма обширная программа испытаний, которая, впрочем, ничем не отличается от применяемых другими производителями. Мастера оценивают состояние ЛКП, проверяют геометрию подвески, работу рулевого управления, тормозной системы, а также герметичность салона и светотехнику.
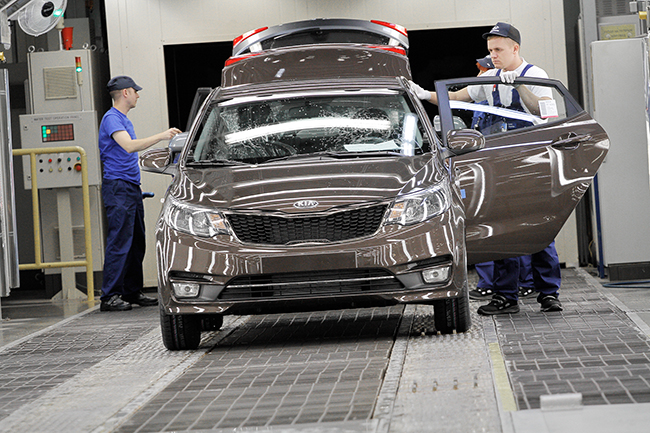
Далее авто выгоняют на улицу, где расположен коротенький тестовый полигон. Все испытания и проверки занимают около двух часов. В итоге на путь от куска металла до полноценного, готового к эксплуатации автомобиля затрачивается примерно 18 часов.
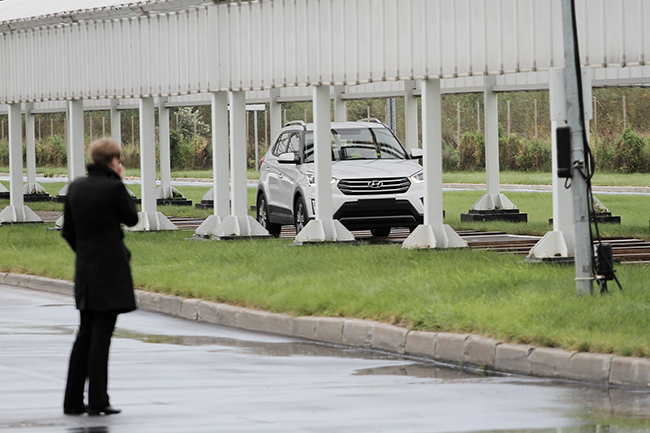
В заключение хотелось бы ответить на вполне резонный вопрос: так насколько же Hyundai, производимые в Питере, российские? Примерно на 46 %. Процент локализации хоть и кажется не очень-то и большим, но на самом деле весьма солидный.
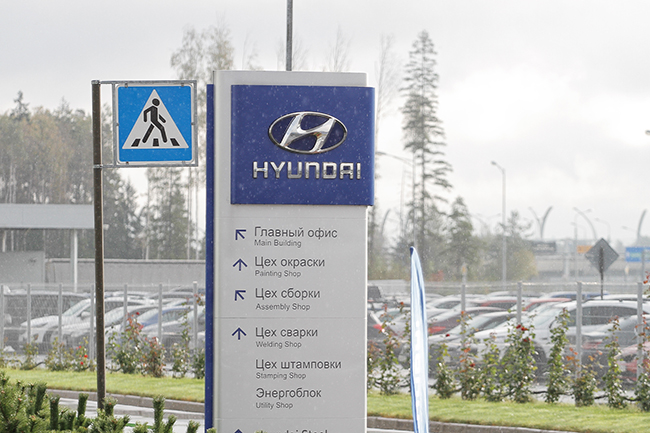